Mastering Cost Risk with the CRED Model: A New Approach to Managing Uncertainty
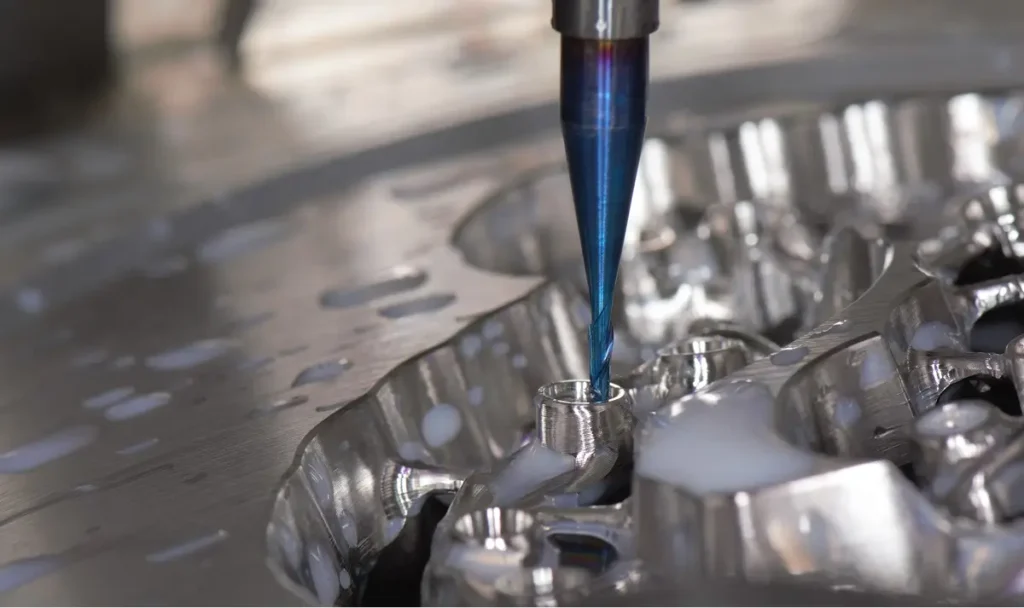
Table of Contents
Manufacturing leaders face intense pressure to deliver high-quality products at competitive prices. The challenge of balancing performance, cost, quality, and speed-to-market is particularly intense in industries such as aerospace and defense, where traditional materials and processes often carry high costs.
Unmanned Aerial Vehicles (UAVs) illustrate this clearly. From large defense-oriented drones to smaller, budget-friendly surveillance or delivery models, the UAV market is rapidly evolving. Manufacturers are revisiting their design and production methods to meet growing demands for affordability without compromising performance. Software solutions like SEER® by Galorath have become crucial in enabling manufacturers to analyze trade-offs in materials and processes and help determine optimal solutions for cost and performance. SEER is a project, cost, schedule and risk estimation platform. SEER for Manufacturing (SEER-MFG™), its manufacturing-focused solution, provides detailed cost modeling for parts, assemblies, and production systems.
Manufacturers who utilize SEER-MFG can better evaluate alternatives, streamline their processes, and deliver competitive products with greater speed and accuracy.
The Challenge: Legacy Manufacturing Processes
One of the biggest hurdles for aerospace manufacturers is their reliance on legacy processes and materials. These methods have been in place for decades—some dating back to the early days of aviation. While they’ve served their purpose in delivering reliable, high-performance products, they’re often over-engineered for modern applications.
For UAVs, especially smaller, attritable systems that don’t need to last 20+ years or endure extreme operational conditions, these traditional standards are simply too expensive and unnecessary. In many cases, manufacturers are using the same materials and processes for both high-end military aircraft and low-cost commercial UAVs, resulting in inefficient production and bloated costs.
To stay competitive, manufacturers need to rethink their approach. This means exploring new materials and processes that balance performance and affordability—a task that can feel overwhelming without the right tools.
The Solution: SEER-MFG for Cost-Effective Trade-Off Analysis
This is where SEER-MFG enables manufacturers to assess alternative materials and processes, providing a clear picture of how different choices will impact production costs, timelines, and overall value.
For instance, many manufacturers are moving away from traditional methods like sheet metal fabrication or hand-laid composite construction, which require extensive manual labor and expensive equipment. Instead, they’re adopting advanced processes such as:
- VARTM (Vacuum-Assisted Resin Transfer Molding) and RTM (Resin Transfer Molding) for composites
- Thermoformed or molded thermoplastics, which reduce the need for machining and assembly
- Adhesively bonded components, replacing traditional drilled and fastened joints
These changes can reduce both material costs and production times significantly. But without a way to accurately predict the cost and performance implications of these decisions, it’s hard for manufacturers to justify the switch. That’s where SEER-MFG stands out because it simplifies the evaluation process and helps manufacturers make data-driven decisions with confidence.
A Real-World Example: The Composites Affordability Initiative (CAI)
A great example of the benefits of alternative manufacturing processes is the U.S. Government’s Composites Affordability Initiative (CAI). This program demonstrated that combining larger molded components with adhesively bonded joints (instead of traditional fastened assemblies) could dramatically reduce the cost of aircraft structures.
By reducing the number of individual parts and eliminating costly drilling and fastening steps, manufacturers achieved significant savings without compromising structural integrity. SEER-MFG allows manufacturers to conduct similar trade studies with ease, comparing traditional methods to newer alternatives and quantifying the cost and time savings they offer.
Imagine having the ability to run these types of studies quickly and adjust your manufacturing strategy on the fly. SEER-MFG not only makes this possible but also opens the door to new possibilities for innovation and production improvements.
How to Get Started
For program managers, budget managers, and cost engineers, the question isn’t whether to explore new materials and processes, it’s how to do it without adding unnecessary risk.
Here are some practical steps to begin your journey:
- Audit Your Current Processes – Identify areas where legacy processes are driving up costs unnecessarily. Focus on processes that are highly manual or require expensive, specialized equipment.
- Explore Alternatives – Consider adopting new materials and production methods, especially for components that don’t require extreme durability or precision.
- Use SEER-MFG for Trade-Off Analysis – Leverage SEER-MFG to model the costs of alternative materials and processes. The tool provides a detailed breakdown, helping you understand how each choice will impact your budget and schedule.
- Run a Pilot Program – Start with a small pilot project to validate your assumptions and refine your approach before scaling up.
- Monitor and Iterate – Keep track of your results and use the data to continuously improve your processes. SEER-MFG makes it easy to revisit your models and adjust your assumptions as needed.
The Bottom Line
Manufacturers can’t afford to remain with the status quo. Galorath’s platform of solutions, including SEER-MFG, enables manufacturers to reduce processes, reduce costs, and deliver products with greater speed and accuracy. For organizations in highly demanding industries, such as aerospace and defense, achieving greater accuracy and agility in manufacturing is critical.
For manufacturers, especially in sectors like aerospace and defense, where production improvements and precision are critical, solutions like SEER-MFG aren’t just beneficial, they’re necessary. For those aiming to streamline costs and improve manufacturing agility, the path forward with SEER-MFG has never been clearer.
So, what’s preventing your organization from taking the next step? With the right solutions and processes readily available, all you need is the commitment to adapt and the desire to create a more efficient, agile manufacturing operation.
10 Step Estimation Process Sample Checklist
View our 10 Step Estimating Process Checklist. This checklist should be tuned to the individual company’s needs and suggestions.
Estimating Total Cost of Ownership (TCO)
Find out how you can use Total Cost of Ownership (TCO) model to create an estimate which includes all the costs generated over the useful life of a given application.
Should Cost Analysis
Learn how Should-Cost Analysis can identify savings opportunities and drive cost efficiency in procurement and manufacturing processes.
ROM Estimate: The First Step Towards a Detailed Project Plan
Find out what ROM (rough order of magnitude) estimate is and why is it a crucial element of every project planning cycle.
Software Maintenance Cost
Find out why accurate estimation of software maintenance costs is critical to proper project management, and how it can make up to roughly 75% of the TCO.